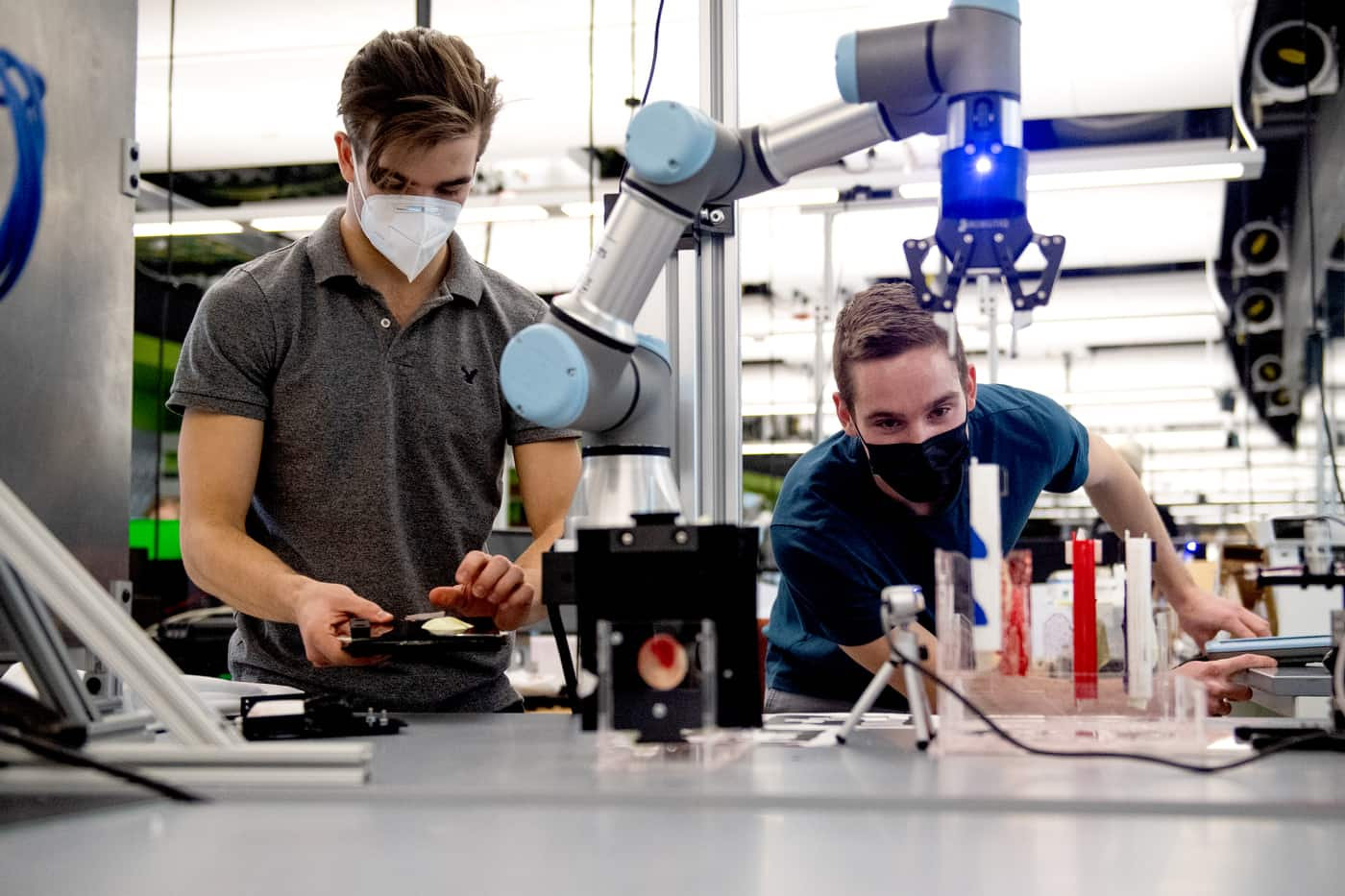
ARM Institute COVID-19 Focused Robotics Projects Mitigate the Current Pandemic and Create a Foundation for Robotic Solutions for Future Crises
On August 30, the ARM Institute hosted a public, virtual Summit showcasing the nine projects and their dual uses for industry and the Department of Defense (D0D)
September 20, 2021 – In the summer of 2020, the U.S. Department of Defense (DoD) entrusted the ARM (Advanced Robotics for Manufacturing) Institute with the important mission of finding robotic solutions to mitigate the COVID-19 pandemic and create a critically needed technical foundation to respond to future similar crises. The ARM Institute engaged with its 300+ member consortium to solicit impactful project ideas, ultimately initiating nine robotics projects through a Special ARM Institute Project Call with funding provided by the Office of the Secretary of Defense.
The ARM Institute is the nation’s leading collaborative in robotics and workforce innovation, working at the confluence of industry, government, and academia. Structured as a public-private partnership, the ARM Institute and its member organizations accelerate robotic technologies and education solutions to strengthen the U.S. industrial base and secure U.S. manufacturing resiliency.
The projects focused on several critical areas, including facility and surface disinfection, COVID-19 testing, the production and quality assurance procedures for personal protective equipment (PPE) production, and the use of robots in building temporary structures that can support hospital efforts.
The ARM Institute rapidly responded to the Department of Defense’s need to address COVID-19 by forming numerous national teams, drawing from diverse industries and technologies to address the myriad of supply chain shortages. This is highlighted by a few of the key statistics listed below:
- Rapid contracting with 45 days from the Project Call release to project start
- Projects executed in 12 months
- 13 states and Puerto Rico engaged
- 23 unique organizations participated across the nine projects
Details on the impact generated from each project are included with the project descriptions outlined later in this press release.
“We are honored to have been entrusted with COVID-19 mitigation by the Department of Defense,” stated Ira Moskowitz, ARM Institute CEO, “The quick execution of these projects and the successful results demonstrate the ARM Institute’s ability to rapidly respond to national needs by leveraging our diverse ecosystem of experts.”
“We are thankful to our project teams who were instrumental in our effort to support the Department of Defense,” noted Cara Mazzarini, ARM Institute Technology Portfolio Manager, “After seeing such positive initial results, we are confident that the technology will continue to be refined and implemented in ways that will improve how our nation responds to future crises.”
On August 30, 2021, the ARM Institute hosted a virtual technical summit exploring these projects on robotics, highlighting impact stories, showcasing project demonstrations, and facilitating networking between attendees and the project teams. The Summit featured a keynote presentation from Mr. Rob Gold (Director, Technology and Manufacturing Industrial Base, Office of the Under Secretary of Defense Research and Engineering), presentations from each project team, and afternoon networking to connect those interested in leveraging project outputs with the teams. The videos below were shown during the event. Will link the embed the videos within each project section. The public can access an archive of the event here. Note that you may need to enable cookies to view the event recording. Email [email protected] if you need further assistance.
Read more about the individual projects below:
Rapid PPE Production through Automation & Robotics
Impact: The outputs from this project reduced the number of human operators needed and increased efficiency, reduced cycle time, increased production throughput, improved robustness via vision-based fault detection and vision guided robotic operation and use of an Edge AI based module as a service to reduce upfront cost of buying equipment.
Description: The COVID-19 pandemic has exposed critical vulnerabilities in the global health care supply chain. At the beginning of the pandemic, U.S manufactures were unable to meet the significant demand for Personal Protective Equipment, resulting in shortfalls and long lead times. This project improves existing automated mask production in the US by including robotic automatic visual inspection, picking-and-sorting, and end-of-line packing and palletizing.
Project Team: Siemens Corporation Corporate Technologies (Principal Investigator), Henderson Sewing Machine Company, Yaskawa Motoman, HomTex Inc
Built-By-Bot: Customized Mask Assembly using Robots
Impact: This project enables custom robotic mask production anytime, anywhere. It also increased the use of automation in an industry that continue to relay primarily on manual labor
Description: The Center for Disease Control (CDC) has identified cloth masks as playing a vital role in slowing the spread of COVID-19, but the supply has not been able to keep up with the demand. Robotic sewing presents a technical challenge because it requires the manipulation of flexible materials, fine motor control, and precise part recognition. This project will build upon the outputs from other ARM robotics projects to automate the robotic production of cloth face masks for personal protective equipment (PPE).
Project Team: Siemens Corporation Corporate Technologies (Principal Investigator), Henderson Sewing Machine Corporation, Sewbo Inc, Bluewater Defense, Industrial Sewing and Innovation Center (ISAIC)
Swarm Robotics for Large Structure Manufacturing
Impact: Pvilion believes that this technology will help them better respond to DoD needs and manufacture the tents domestically. The robots also relieve the strain on human workers.
Description: COVID-19 has highlighted the urgent need to rapidly deploy negative pressure spaces. These air supported structures are rapidly deployable with performance advantages over traditional tents, and are ideal for use as expeditionary hospitals, quarantine facilities, housing, and other disaster relief or military applications. Production of these structures is labor-intensive but can be expedited with the development of robotic technology to aid manufacturing personnel with moving and manipulating heavy, flexible materials. This project aims to solve the problem of moving and manipulating a large, heavy, flexible material over a large area by developing a fleet of self-aware, human-directed robotic platforms to take on the hard work of moving the material around the production floor. This manufacturing technology will help team member Pvilion produce a “hospital in a shipping container” that can be set up in a parking lot with a crew of 8-10 and a forklift in only 72 hours.
Project Team: Rensselaer Polytechnic Institute (Principal Investigator) and Pvilion
Automation of Characterization and Evaluation (ACE) in PPE Manufacturing
Impact: This project created technology that enables the rapid expansion of a USA industrial base in the category of AAMI tested medical PPE. The project also resulted in the ability to perform three separate quality assurance tests in-house by integrating robotics and automation into the quality assurance processes for PPE manufactured in the US. This will help to addresses supply chain variability issues.
The technology could also be used for fluid penetration tests, flammability tests, liquid barrier tests. It also has applications in laboratory automation, medical device manufacturing, biopharmaceutical, and furniture and garment manufacturing.
Description: The quality assurance procedures for Personal Protective Equipment (PPE), such as facemasks, is labor intensive and time consuming. Sample testing of PPE has become a priority not only in manufacturing plants but also at medical centers. The national labs providing validation testing for PPE are reporting lead times up to 75 days due to lack of qualified technicians and overwhelming volume of new requests. This project aimed to develop a robotic system to automate the quality assurance tests for PPE inspection, thus improving the performance, productivity, and efficiency of PPE manufacturing in the United States.
Project Team: Northeastern University (Principal Investigator), Merrow Manufacturing, and Boston Engineering.
Robotic Application of Anti-Microbial Copper Coatings
Impact: The project resulted in a production ready semi-automated Robotic cold spray to provide self-disinfecting high touch items. The set-up is ready to be used “as a tested” system (VRC Metal Systems spray, NX CAM Robotics, Sinumeric Controler, Comau Robot with RunMyRobot.). The set-up is also easily customizable. The project also advanced the technology closet to an easy-to-use stand-alone system for the scanning and spraying of miscellaneous parts.
The robotic application of cold spray also has many other applications in repair, additive manufacturing, and more. The system could be adapted to mobile robots for scanning and coating of fixed assets, large objects.
Description: Copper-coated surfaces rapidly kill coronaviruses like COVID-19, but these have not been widely manufactured due to low demand. However, the pandemic has highlighted the need for self-disinfecting surfaces. Robotic cold spraying of copper will enable rapid production to meet the new demand. Wide adoption of copper-coated surfaces will reduce the spread of COVID-19 without the need for frequent cleaning. The robotic application of copper coating will improve the manufacturability of these parts. This project developed a robotic anti-microbial copper application system (cold spray), integrating a scanner and developing an automated path generation and QA tools to apply the copper coating to components like a doorknob, hospital bench, cart, handrail, etc.
Project Team: Siemens Corporation Corporate Technologies (Principal Investigator), VRC Metals System
Rapid Robotic Diagnostic Kit Discovery (R2D2)
Impact: This system accelerates test strip development by 2-3x, improves process quality and reliability, and reduces the number of technicians needed. The technology can be extended to any LFA based test kit development process, is easily scalable, and helps to respond rapidly to outbreaks like COVID-19.
Description: While many tests for COVID-19 have been developed, the U.S still has not reached the scale necessary for effective management and control. COVID-19 Polymerase Chain Reaction (PCR) tests have long turnaround times (2-3 days for lab results). Rapid development of COVID-19 Lateral Flow Assay (LFA) tests would dramatically aid the United States’ efforts towards large-scale testing for current and future pandemics. LFA test strip evaluation requires at least two technicians – one to run the assay and one to interpret results using analyzers that image and quantify individual strips. This project developed a solution utilizing advanced vision systems and flexible robots to accelerate LFA test development by automating LFA test-strip evaluation.
Project Team: Siemens Corporation Corporate Technologies (Principal Investigator), Maxim BioMedical Inc, and Siemens Healthineers
Autonomous Robotic Spraying and Disinfection in Warehouses & Shipyards
Impact: This application reduced system setup time and effort through the autonomous collection of a map, an intuitive operator user-interface for general users, and a portable operation interface that is accessible from any browser.
The system also ensured a safe and healthy working environment with minimal impact on operations through automated disinfecting routines using autonomous navigation and robust visual perception, the use of a scalable platform to augment disinfection capabilities of human janitorial staff, and consistent and precise spraying of known high-touch surfaces to reduce transmission of pathogens.
The system also developed reusable and scalable technology modules by leveraging both open-source and commercially-available software and the demonstration of a relationship to, and coexistence with, other commercial products.
Project Description: Logistics and support operations have played a vital role in supporting the nation by supplying medical supplies and essential goods to millions of Americans. To control the spread of COVID-19 in these facilities, more frequent and reliable disinfection is required. This project developed an autonomous warehouse disinfection system that can automatically navigate, locate, and disinfect heavily touched surfaces and potentially contaminated areas. This process minimizes the human role in potentially harmful disinfecting procedures while reducing costs.
Project Team: Siemens Corporation Corporate Technologies (Principal Investigator) FedEx Corporation, Yaskawa Motoman
Mobile Autonomous Industrial Disinfector (MAID)
Impact: The commercially deployed solution is projected to cost less than $100K.
Return-on-investment is projected to take between several weeks to four months, depending on environment size/ complexity and retreatment frequency.
Disinfecting 10,000 ft2 is expected to take just eight hours based on: prototype operating speeds of 2.15 ft2/sec, the 6ft diameter effective UV-C tower, moderate number of areas requiring secondary disinfection/region, using one treatment per region, and handling large spaces with multiple robots.
Description: Due to the rapid transmutability of COVID-19, frequent surface disinfection is required for businesses and workspaces to operate safely. The current method of manual cleaning is not ideal because it puts another person into the space who could get sick or transmit the virus. This project developed an autonomous mobile robot with a mounted collaborative multi-axis robotic arm capable of manipulating both a disinfection system and a sensor suite. The system identifies areas that need disinfecting, execute the disinfecting process, and keep records of the cleaning tasks completed.
Project Team: Lockheed Martin Advanced Technology Laboratories, GrayMatter Robotics, Southwest Research Institute (SwRI), Lockheed Martin Rotary Mission Systems
Human-Assisted Autonomous Mobile Capability for Multi-Room Disinfecting Robot (HAAMSDR)
Impact: The system saw a 27.2% reduction in human work when using the same number of systems as baseline, limiting human exposure to infection.
When using the same amount of human involvement as the baseline, the system resulted in a 19.3% increase in the area disinfected and a 28% improvement in human utilization.
Description: Schools, offices, military bases, and manufacturing floors need to be disinfected between shifts to minimize the spread of COVID-19. The Decon–X (DX1) disinfecting system has proven its effectiveness in Europe, but currently lacks the mobility and autonomy to disinfect spaces without an operator. An automated solution is required to ensure workers return to a COVID-free environment each day. This project added mobile autonomous capabilities to the DX1 room disinfection system to automate the consecutive treatment of multiple rooms and spaces within workplaces. The addition of mobility and autonomous navigation to the DX1 enables the robot to move from room to room and perform a series of treatments with little to no human intervention.
Project Team: QinetiQ North America (Principal Investigator), MassRobotics
Next steps:
Interested in leveraging technology generated from these projects? Contact [email protected] and the ARM Institute will get you connected.
Stay updated on ARM Institute funded projects, upcoming events, and more by subscribing to our mailing list below!
[su_button url=”https://arminstitute.us15.list-manage.com/subscribe?u=47b1073577ae90bb0b12c2f04&id=d4a694e3f8″ target=”blank” background=”#000000″ size=”9″ center=”yes” radius=”0″]JOIN OUR MAILING LIST[/su_button]
About the ARM Institute
The ARM (Advanced Robotics for Manufacturing) Institute is a Manufacturing Innovation Institute (MII) funded by the Office of the Secretary of Defense under Agreement Number W911NF-17-3-0004, and part of the Manufacturing USA® network. The ARM Institute leverages a unique, robust, and diverse ecosystem of consortium members and partners across industry, academia, and government to make robotics, autonomy, and artificial intelligence more accessible to U.S. manufacturers large and small, train and empower the manufacturing workforce, strengthen our economy and global competitiveness, and elevate national security and resilience. Based in Pittsburgh, PA since 2017, the ARM Institute is leading the way to a future where people & robots work together to respond to our nation’s greatest challenges and to produce the world’s most desired products. For more information, visit www.arminstitute.org and follow the ARM Institute on LinkedIn and Twitter.