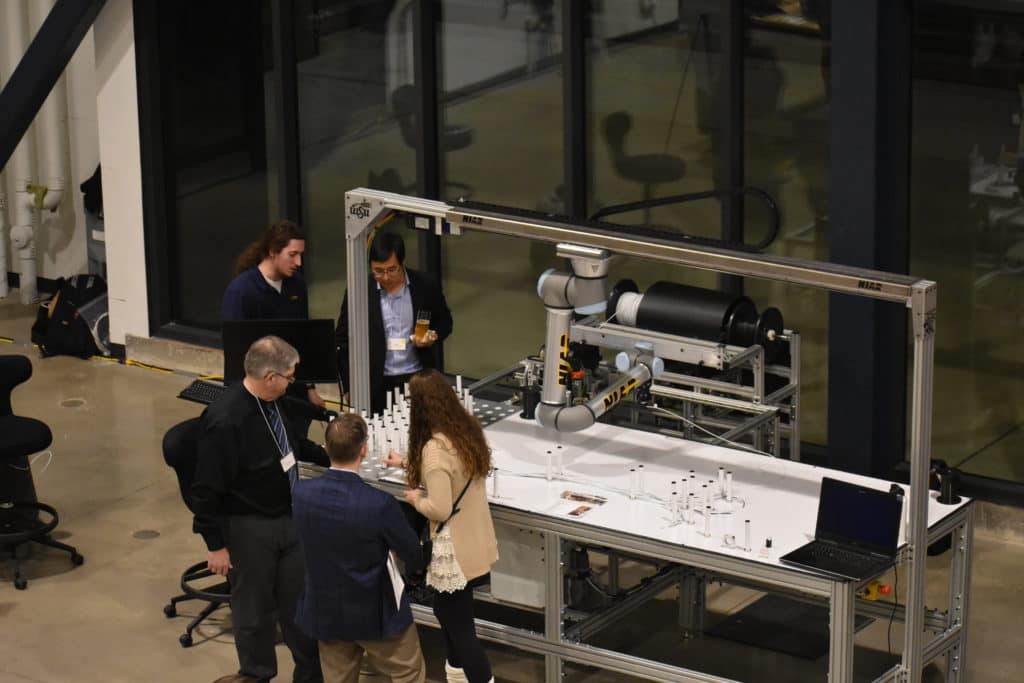
Wire Harness Assembly Process Project Background
Today’s wire harness assembly process is a time-intensive, manual process that results in inconsistent product quality and high prices. This robotics project sought to reduce wire harness assembly costs by using collaborative robots to lay wiring through the development of a unique end effecter. The technology integrates into existing ECAD, increasing the ease of integration and allowing for adoption by other markets, enabling other industries harness automation to speed up manufacturing processes.
Wire Harness Assembly Process Project Objective
Reduce the cost of the wire harness assembly process by automating the manufacturing process via collaborative robots.
Wire Harness Assembly Process Project Technical Approach
This project will lower the cost of the wire harness assembly process via robotics and automation. Collaborative robots will be able to lay wiring through the development of a unique end effector. The project will also:
- Integrate into preexisting ECAD for laying wire on preexisting foam boards
- Increase versatility and flexibility through the utilization of preexisting foam boards, multiple cable varieties, automated labeling, and quick change tool heads
The project outputs have the potential for adoption by other markets.
Wire Harness Assembly Process Project Participants
Wichita State University (Principal Investigator), Lockheed Martin